Los plásticos para vehículos eléctricos
Aplicaciónes > ► Vehículos eléctricos
Los plásticos para vehículos eléctricos
El moldeo por inyección de plástico es una parte esencial de la cadena de suministro y el proceso de fabricación de las empresas de automóviles eléctricos. Si bien generalmente asociamos los automóviles con metal en lugar de plástico, el moldeo por inyección de automóviles es una parte creciente de la industria, gracias en parte al auge de los automóviles eléctricos. Si bien el exterior de un automóvil sigue siendo principalmente de metal, las empresas de automóviles están cambiando cada vez más del metal al plástico para los componentes internos. El aumento en el consumo de plásticos como polipropileno (PP) y poliuretano (PU) en los últimos años ha sido parcialmente compensado por la disminución del consumo de plásticos de ingeniería, con PP y PU representando alrededor del 50% del consumo total de plástico en vehículos. Se espera que el consumo de plásticos de ingeniería disminuya debido al menor requerimiento de estos plásticos en aplicaciones bajo el capó para vehículos eléctricos, ya que la resistencia a altas temperaturas de los polímeros de ingeniería no se requiere en la misma medida que con los motores de combustión interna. En cambio, se utilizarán poliamidas para soportes de batería y carcasas en los vehículos eléctricos. La demanda de polipropileno seguirá creciendo a medida que encuentre nuevas aplicaciones en el interior y exterior de los automóviles, y debajo del capó reemplazando algunas partes metálicas. Además, el crecimiento también se verá impulsado por una mayor producción de vehículos eléctricos, que requerirán piezas más ligeras para ayudar a compensar el peso de las baterías pesadas. El consumo de PE también se ha mantenido estable, ya que los tanques de gas de HDPE ya han penetrado en el mercado de tanques de gasolina, desplazando al acero en los países desarrollados. Sin embargo, los vehículos eléctricos pueden utilizar más PE en las piezas del motor, ya que los motores de batería eléctricos no requieren el rendimiento a alta temperatura de los polímeros de ingeniería..
Electrónica del tren motriz: materiales para componentes de automóviles eléctricos con menos deformaciones, menos densidad y menos electrocorrosión
Los coches eléctricos están provocando un cambio de componentes semicristalinos bajo el capó hacia materiales amorfos. Desde enchufes de alto voltaje hasta sensores, convertidores, inversores y barras colectoras, las piezas del tren motriz totalmente eléctricas exigen una mayor estabilidad dimensional, deformación limitada, menos absorción de humedad y ausencia de corrosión electrónica. PC, PC/ABS retardados a la flama, brindan a los fabricantes de componentes del tren motriz de vehículos eléctricos una amplia selección de materiales que cumplen con estos criterios, incluida la contracción isotrópica y la retardancia de llama a base de fósforo sin electro corrosión.
Los beneficios del moldeo por inyección para vehículos eléctricos
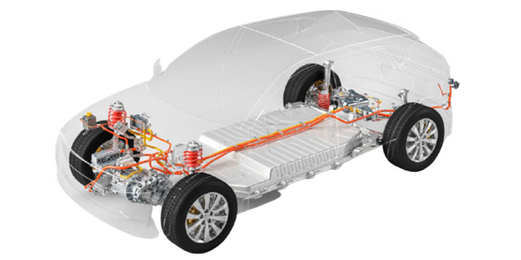
¿Por qué el moldeo por inyección de plástico es vital para los fabricantes de vehículos eléctricos? Estas son solo algunas de las razones por las que las empresas de automóviles eléctricos y sus fabricantes de equipos originales están presionando para hacer la transición del metal al termoplástico para muchos componentes clave:
Las piezas de plástico ayudan a reducir el peso. La mayor ventaja del moldeo por inyección de componentes internos para los fabricantes de equipos originales de vehículos eléctricos es también la más simple: el peso. El metal pesa más que el plástico. Para los autos eléctricos, cada kilo extra es importante, ya que el peso afecta el rango de recorrido que el vehículo puede alcanzar entre cargas. Los vehículos eléctricos más pesados requieren más energía para moverse, lo que significa que también agotan sus baterías más rápidamente. Los vehículos más livianos pueden ir más lejos con una sola carga, lo que los hace más atractivos para el conductor promedio, mejorando el retorno de la inversión y ayudándolos a cumplir con las regulaciones cada vez más estrictas para la eficiencia del vehículo. El uso de plástico en lugar de metal puede permitir a las empresas de automóviles eléctricos reducir el peso de sus vehículos hasta en un 30 por ciento.
Las piezas de plástico son más asequibles. Otro beneficio significativo de trabajar con un fabricante de plástico para termoplásticos automotrices es que las piezas de plástico moldeadas por inyección son más baratas de producir que sus contrapartes de metal. Cambiar las piezas de metal por componentes de plástico es una forma de reducir el costo de producción del automóvil, lo que permite a las empresas de automóviles eléctricos bajar sus precios y competir de manera más efectiva en un mercado abarrotado.
Las piezas de plástico tienen características sorprendentes. Aquellos que están en contra del uso de piezas moldeadas de plástico en los vehículos asumen que los costos más bajos conducen a diseños más baratos o un rendimiento inferior. Incluso existen algunas preocupaciones de que cambiar a diseños de vehículos basados en plástico tenga un impacto negativo en la seguridad o durabilidad. En verdad, los termoplásticos de calidad pueden ofrecer altos niveles de resistencia a la tracción, resistencia al calor, flexibilidad, resistencia al impacto y otros atributos positivos. Estas características no solo significan que los componentes de plástico son tan confiables como el metal, sino que también explican por qué los fabricantes de equipos originales utilizan plástico para una variedad versátil de aplicaciones, desde carcasas de baterías hasta cubiertas de tableros y paneles externos. A medida que los vehículos eléctricos ganan más participación en el mercado de la industria automotriz, los fabricantes deben ser creativos y encontrar formas de reducir el peso y el precio de sus vehículos al tiempo que aumentan la eficiencia y el alcance. Como fabricante de plástico con una amplia cartera de productos, podemos ayudar a su empresa a descubrir los beneficios del moldeo por inyección para vehículos eléctricos.
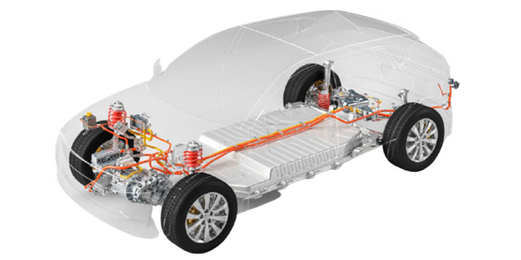
Juntas y Sellos
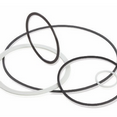
Materiales ; Elastomeros, TPV, SEBS
_______________________________________________________________________________________________________________________________________________________
Caja de batería para vehículos eléctricos
Empacar muchas celdas de carga rápida en una batería de automóvil eléctrico significa tener componentes que son retardadores de llama, resistentes a los impactos y robustos tanto a bajas como a altas temperaturas. Nuestro mezcla XBLEND B 2500AE es una excelente solución para los portaceldas y los módulos de batería EV, permaneciendo estable hasta 85°C, asegurando una eficiencia operativa óptima , bajo peso. También cumple con la clasificación UL94 V-0 de retardo de llama. Nuestra resina XBLEND B 2500AE tiene la durabilidad necesaria para la carcasa protectora y se ha demostrado que resiste vibraciones e impactos, incluidas las condiciones de prueba de abuso. Tiene unadensidad reducida y menor peso, equilibrio rigidez-tenacidad, resistencia al calor, adherencia mejorada a componentes blandos. Este nuevo PC/ABS también ofrece una ventaja de costos en comparación con el PC/ABS tradicional. La densidad reducida, el alto flujo y las ventajas de costo del ABS/PC para esta aplicación compuestos ignífugos, robustos y de alto rendimiento para coches eléctricos.
Materiales: XBLEND B 2500AE
Propiedades peculiares: Resistencia al calor, resistencia al impacto, baja emisión, flexibilidad.
_______________________________________________________________________________________________________________________________________________________
Tanques de combustible
Los tanques de combustible de plástico se usaban tradicionalmente en vehículos con motores de combustión interna. Actualmente, los vehículos eléctricos híbridos que tienen un ICE, así como una batería, también constan de tanques de combustible de plástico. Estos tanques de combustible de plástico ayudan a reducir el peso, que es uno de los requisitos clave de la industria del automóvil. Los vehículos eléctricos de autonomía extendida cumplen con el requisito de autonomía extendida de la batería de los consumidores para hacer funcionar vehículos eléctricos en largas distancias.
_______________________________________________________________________________________________________________________________________________________
Embalaje de la batería
Muchos consideran que la batería es el mayor desafío porque debe ser liviana, debe estar protegida de los elementos y los daños, y debe alimentar el vehículo durante el mayor tiempo posible. El portabaterías de los vehículos eléctricos es absolutamente fundamental para una gestión térmica eficaz. Evitar el sobrecalentamiento de las baterías es una prioridad fundamental para los fabricantes de vehículos, ya que los cambios químicos provocados dentro de la batería tienen consecuencias extremadamente dañinas. Además, la carga también puede crear problemas. Cuanto más tiempo pasa completamente cargado, más rápidamente se acumula la resistencia interna y surgen problemas similares. Siga así con el tiempo y la batería se volverá inútil. Una vez más, el énfasis en la gestión térmica innovadora es clave. La carga a alta velocidad puede sobrecalentar rápidamente las baterías de los automóviles eléctricos, que deberían funcionar por debajo de los 42°C para una máxima eficiencia y una vida útil más prolongada. Los portabaterías deben ofrecer una estructura protectora para detener los daños por impacto y también una aplicación para mejorar la gestión térmica. Adaptamos el embalaje de la batería a su gestión térmica. PC/ABS retardados a la flama retiene más del 91% de su resistencia al impacto cuando aloja refrigerantes de batería de agua / glicol. PC/ABS retardados a la flama está diseñado para sistemas refrigerados por aire. Los grados específicos de PC/ABS tienen resistencia química a los materiales de cambio de fase. Los grados de PC que disipan el calor ofrecen una mayor conductividad térmica mientras mantienen buenos niveles de flujo y ductilidad.
Materiales: XBLEND B 3500AE
_______________________________________________________________________________________________________________________________________________________
_______________________________________________________________________________________________________________________________________________________